Employee training using TAAF matching funds helped to transform GEM
“ISO 13485 certification and all the other training definitely broadened our basis for getting more business.”
—Mike Coleman, Quality and Service Manager
Background
GEMCITY Engineering and Manufacturing*, located in Dayton, Ohio, is a well-known contract manufacturer and supplier of automation equipment. They focus on making highly-engineered products and equipment for a range of industries, including aerospace, defense, medical, and semiconductors. Founded in 1936, the company celebrated its 80th anniversary in 2016.
The company had a facility in Thailand to better serve its multi-national customers operating there and to provide a value added resource of manufacturing for proven machine designs.
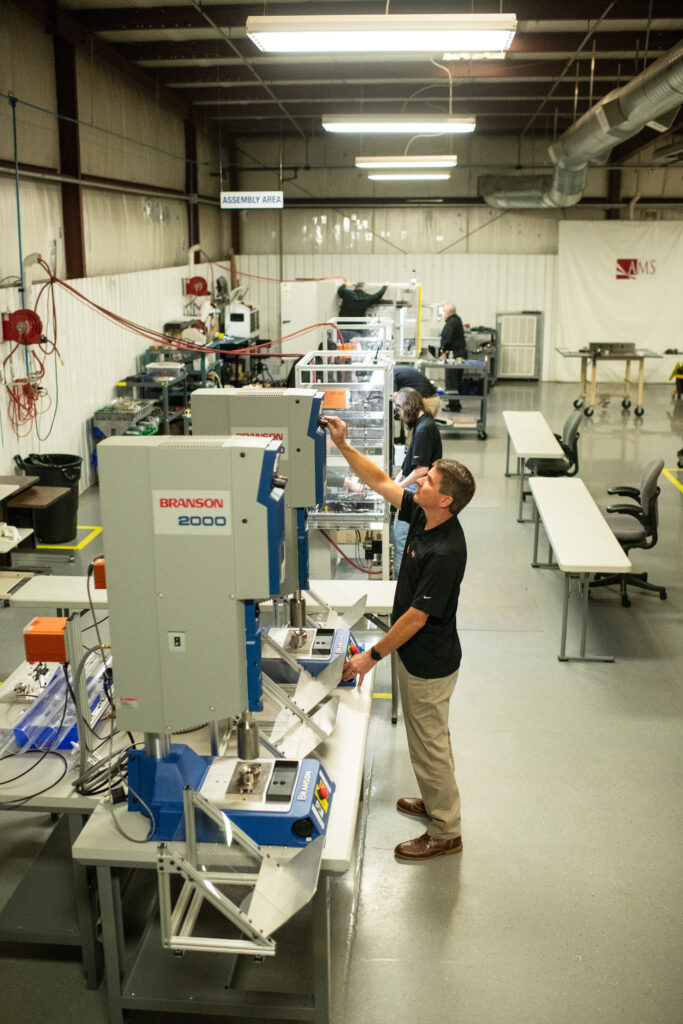
Nevertheless, increasing imports, along with the recession of 2009, dramatically reduced GEM’s sales and profitability and they joined the TAAF program.
Approach
GLTAAC noted the company had strong systems and strong engineering skills. GEM wanted to support its diversification efforts into the medical markets, where it had identified opportunities and had acquired Vistek, a Pennsylvania firm supplying implants, orthopedics, and other medical devices.
GLTAAC recommended obtaining ISO 13485 certification, even though certification was not required by the firm’s medical customers at the time.
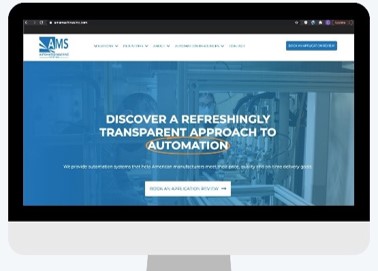
GEM used TAAF co-funding to engage consultants to help shepherd the company to ISO 13485 certification and also provide a battery of additional related quality training. This training was done to meet the needs of various customers in specific areas, such as FDA compliance, NEC (National Electrical Code) compliance, clean room setup and training, etc. and to position the company to better acquire future business. The employee development resulting from this whole effort proved to be pivotal for the company.
Results
GEM was able to double its sales into medical markets (from 5% to 10% of total sales) while improving its gross margin at the same time. Further, its workforce GEM-specializedwas so well trained that it allowed the company to consolidate all medical operations into its Dayton headquarters, reducing overall costs and improving quality at the same time.
“ISO 13485 certification and all the other training definitely broadened our basis for getting more business,” says Mike Coleman, GEM’s Quality and Service Manager. “A lot of prospective customers in the medical field won’t even talk to you unless you are 13485 certified – it’s the first question they ask”.
*In December 2019, GEMCITY merged with Ohio’s Libra Industries